

darkness).ĭuring the diagram development phase, the above categories are modified depending on the needs, some of them may then be omitted or replaced with others. Environment – this group should consider the causes of problems in the workplace (eg.Management – problems related to organization in the company.Method – means a method of performing an activity.Material – problems in this category are typically caused by components.Machine – the most common cause due to the fault of the machine.Man – all activities performed that result in a problem.The most common Cause and Effect schema has five main classification groups: In the next phase, identify the main categories of possible causes of the problem (effect). The defect is noted at the end of the horizontal axis of the diagram. On the other hand, “bones” directly pinpoint the causes of the problem.The next section is the “backbone” that identifies the root causes of the problem.The first is “fish head”, which represents the analyzed problem, or rather failure to meet expectations and non-compliance with the specification.Ishikawa Diagram structureįishbone diagram consists of three parts: It sorts ideas into useful categories instantly. It can be used to organize a brainstorming session. Therefore, the team should consist of people with high specialist knowledge who additionally want to reveal the causes of faults, including those caused by themselves. Plotting the cause and effect chart must be an effort by many employees in the organization, as failure usually comes from different fields of activity.
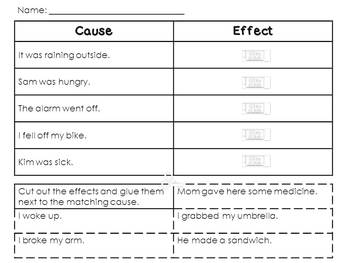
The simplicity and broad functionality of the Ishikawa chart makes it one of the first steps in problem analysis. Usually, we start each qualitative analysis by defining the problem and looking for its causes. Cause-and-effect analysis was discovered by Professor Kaoru Ishikawa, a pioneer in quality management, in the 1960s. It can be successfully used in industry, services, administration and project management. Ishikawa diagram allows to identify the causes of actual or potential failures of various types of projects. The cause and effect chart is one of the main and most popular tools for analyzing and solving quality problems in enterprises. In other words, ishikawa diagrams can help you identify defects in your processes by analyzing causes of an issue. Using fishbone diagrams, all the components that are part of the workflow can be analyzed and hence the problems causing some kind of inefficiencies can be easily and efficiently identified. Cause And Effect) in Excel Ishikawa diagrams, popularly known as fishbone diagram or cause and effect diagram, are mainly used in quality management in order to analyze inefficiencies in workflow processes.
